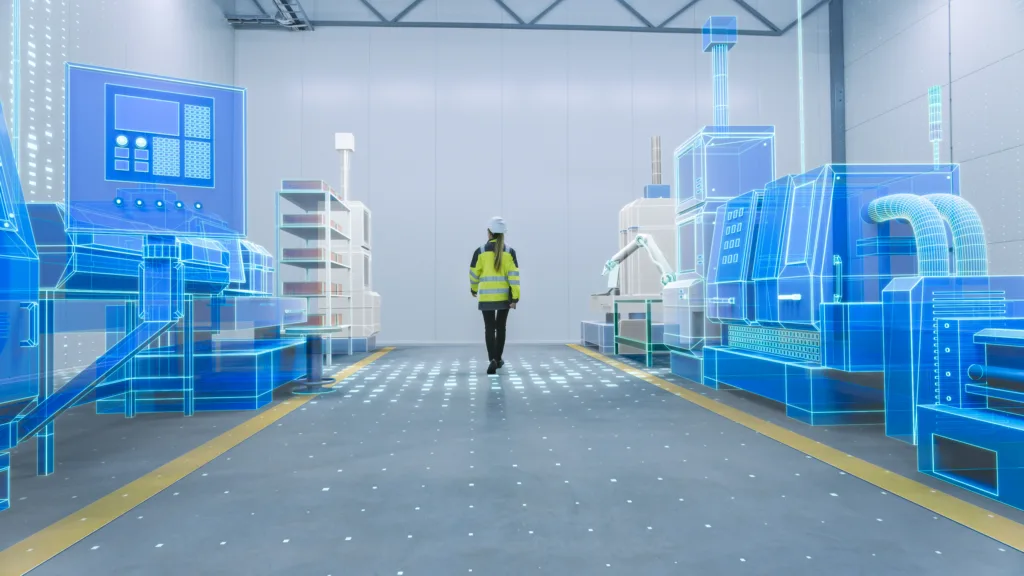
Von der Planung bis zum Recycling
Bereits die einzelnen Anwendungsgebiete des Digitalen Zwillings für Ihre Fabrik weisen häufig eine stark positive Kosten-Nutzen-Bilanz auf.
- Simulation
- High Level Emulation
- Low Level Emulation
- Optimierungsbetrieb
- Anpassungen und Retrofits
Digitale Zwillinge: Von der Planung bis zum Recycling
Die Industrie 4.0 ändert grundlegend die Art und Weise, wie Fabriken funktionieren, und der Digitale Zwilling ist dabei ein Schlüsselbaustein. Doch was verbirgt sich genau hinter diesem Begriff, und wie können Unternehmen von dieser Technologie profitieren?
In diesem Artikel werfen wir einen Blick auf den gesamten Lebenszyklus eines Digitalen Zwillings – von der ersten Planung bis hin zu Anpassungen und Retrofits.
1. Simulation: Den Grundstein legen
Der Digitale Zwilling beginnt meistens mit der Simulation. Bereits in der Planungsphase wird ein grobes Konzept Ihrer Anlage digital nachgebildet. Dies ermöglicht, potenzielle Fehler oder Engpässe im Design frühzeitig zu erkennen und zu beheben. Dabei können auch verschiedene vielversprechende Konzepte verglichen werden. Unternehmen sparen so nicht nur Zeit und Geld, sondern erhalten auch eine solide Grundlage für alle weiteren Schritte.
2. High Level Emulation: Realitätsnahe Tests
Die High Level Emulation bildet die logischen Schnittstellen zu den Leit- und Überwachungssystemen, beispielsweise SAP EWM, detailgetreu ab. Dies sorgt dafür, dass die Systeme genauso funktionieren und getestet werden können, wie in der späteren realen Produktionsumgebung. Fehlerquellen im Zusammenspiel der IT-Systeme werden auf diese Weise bereits vorab minimiert.
3. Low Level Emulation: Risikofreie Validierung
Im nächsten Schritt folgt die Low Level Emulation. Hier werden die steuerungstechnischen Abläufe der Anlage mit geringem Aufwand und minimalem Risiko durch das Einbinden der Steuerungen getestet. Dies ermöglicht es, Optimierungen vorzunehmen und die Prozesssicherheit zu erhöhen, bevor die Produktion startet.
4. Optimierungsbetrieb: Effizienz steigern
Nach dem Produktionsstart hört die Arbeit mit dem Digitalen Zwilling nicht auf. Mit Hilfe des Optimierungsbetriebs können neue Fertigungsstrategien getestet und Leistungssteigerungen erzielt werden. Unternehmen haben so die Möglichkeit, flexibel auf veränderte Marktbedingungen und Produktmixe zu reagieren.
5. Anpassungen und Retrofits: Zukunftssicher bleiben
Industrien müssen sich kontinuierlich anpassen, um wettbewerbsfähig zu bleiben. Der Digitale Zwilling erleichtert die Planung, das Testen und die Umsetzung von Umbauten oder Modernisierungen. Dadurch werden Stillstandszeiten reduziert und die Flexibilität erhöht.
Fazit: Mehr als nur ein digitales Abbild
Der Digitale Zwilling ist weit mehr als nur eine virtuelle Kopie einer Anlage. Er ist ein dynamisches Werkzeug, das Unternehmen dabei unterstützt, ihre Prozesse effizienter, flexibler und nachhaltiger zu gestalten. Von der ersten Simulation über die Produktion bis hin zu kontinuierlichen Optimierungen bietet der Digitale Zwilling unzählige Vorteile, die in der modernen Industrie unverzichtbar sind.
Lernen Sie mehr! Möchten Sie tiefer in die Welt der Digitalen Zwillinge eintauchen? Unsere detaillierte Infografik zeigt Ihnen alle Schritte im Überblick. Jetzt anschauen und entdecken, wie auch Ihr Unternehmen von dieser Technologie profitieren kann.
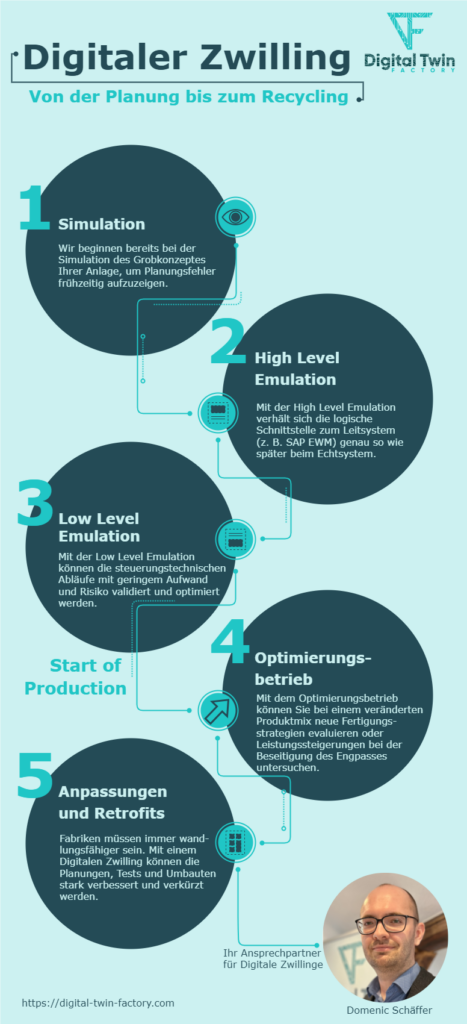
Download
Mehr entdecken
Infografik: Von der Planung bis zum Recycling
Checkliste: Erfolgreiche Einführung eines Digitalen Zwillings im Anlagenbau
Whitepaper: Implementierung von Digitalen Zwillingen: Herausforderungen und Best Practices