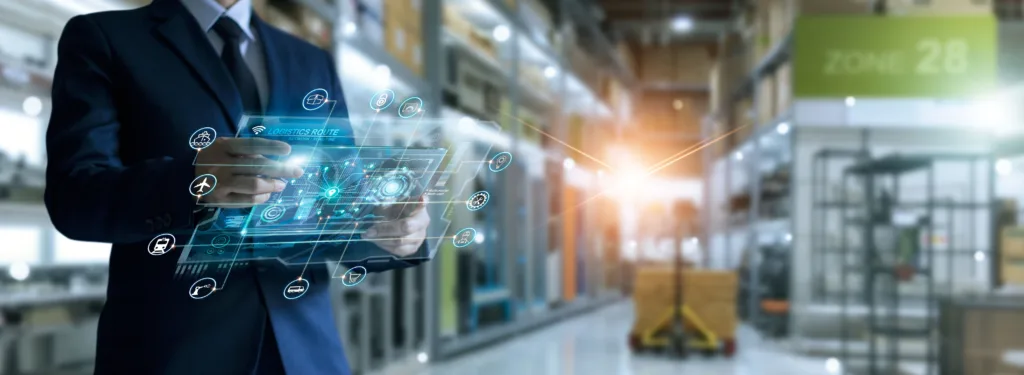
Optimierungsbetrieb
Einsatz des Digitalen Zwillings bietet eine risikoarme, kosteneffiziente und flexible Optimierung der Produktion, ohne dass die reale Anlage beeinträchtigt wird.
- Keine Unterbrechung der Produktion
- Fundierte Entscheidungen
- Erhöhung des Durchsatzes
Optimierungsbetrieb mit dem Digitalen Zwilling: Maximierung der Effizienz nach Produktionsstart
Nach dem erfolgreichen Start der Produktion (SOP) stehen Unternehmen vor der Herausforderung, ihre Fertigungsprozesse kontinuierlich zu optimieren, um wettbewerbsfähig zu bleiben. Der Digitale Zwilling spielt hierbei eine entscheidende Rolle. Indem wir Ihren Digital Twin von den ursprünglichen Plandaten auf die realen Betriebsdaten umstellen, eröffnen sich vielfältige Möglichkeiten, die Produktion effizienter und flexibler zu gestalten.
Umstellung von Plandaten auf reale Daten
Während der Planungsphase wird der Digitale Zwilling mit geplanten und historischen Daten gespeist, um Produktionsprozesse zu simulieren und zu planen. Nach dem SOP ist es jedoch essenziell, den Digital Twin mit aktuellen Echtzeitdaten zu versorgen. Dies gewährleistet, dass das virtuelle Modell die tatsächlichen Betriebsbedingungen und Leistungskennzahlen widerspiegelt.
Durch diese Umstellung können Unternehmen:
- Neue Betriebssituationen vorab testen.
- Genauere Prognosen und Analysen basierend auf aktuellen Daten erstellen.
- Schneller auf Abweichungen reagieren und Anpassungen vornehmen.
Vorteile des Optimierungsbetriebs
Evaluierung neuer Fertigungsstrategien bei verändertem Produktmix
Marktbedingungen ändern sich ständig, und Unternehmen müssen ihren Produktmix entsprechend anpassen. Mit einem auf realen Daten basierenden Digitalen Zwilling können Sie verschiedene Szenarien simulieren:
- Analyse der Produktionsauslastung bei Einführung neuer Produkte.
- Optimierung von Produktionsplänen, um Engpässe zu vermeiden.
- Bewertung der Auswirkungen auf Lieferzeiten und Ressourcenbedarf.
Untersuchung von Leistungssteigerungen durch Engpassbeseitigung
Engpässe können die gesamte Produktion verlangsamen. Durch den Digitalen Zwilling können Sie:
- Engpässe identifizieren und deren Ursachen analysieren.
- Prozessänderungen simulieren, um die beste Lösung zu finden.
- Ressourceneinsatz optimieren, um die Produktionsleistung zu steigern.
Kontinuierliche Prozessverbesserung
- Reduzierung von Ausschuss und Nacharbeit durch frühzeitige Fehlererkennung.
- Steigerung der Produktqualität und Durchsatz durch optimierte Prozessparameter.
- Verlängerung der Lebensdauer von Anlagen durch optimale Nutzung.
Kosteneffizienz und Ressourcenschonung
- Reduzierung von Energieverbrauch durch effiziente Prozesssteuerung.
- Optimierung des Materialflusses, um Lagerkosten zu senken.
- Nachhaltige Produktion durch minimierten Ressourcenverbrauch.
Implementierungsschritte für den Optimierungsbetrieb
Datenintegration
- Sammeln von Echtzeitdaten aus Produktionsanlagen und Sensoren.
- Sicherstellung der Datenqualität durch Validierung und Bereinigung.
Modellanpassung
- Aktualisierung des Digitalen Zwillings mit realen Betriebsdaten.
- Anpassung der Simulationsmodelle an aktuelle Prozessbedingungen.
Simulation und Analyse
- Durchführung von Was-wäre-wenn-Szenarien für verschiedene Optimierungsansätze.
- Analyse der Ergebnisse zur Identifizierung der besten Strategien.
Implementierung von Optimierungsmaßnahmen
- Umsetzung der identifizierten Maßnahmen im realen Produktionsumfeld.
- Überwachung der Auswirkungen und Feinabstimmung bei Bedarf.
Zukunftsausblick
Die kontinuierliche Nutzung des Digitalen Zwillings im Optimierungsbetrieb ermöglicht es Unternehmen, agil und effizient auf Marktveränderungen zu reagieren. Zukünftige Entwicklungen könnten beinhalten:
- Integration von KI und Machine Learning zur automatischen Optimierung.
- Erweiterte Realität (AR) für eine noch engere Verknüpfung von virtueller und realer Welt.
- Globales Netzwerk von Digitalen Zwillingen zur standortübergreifenden Optimierung.
Nutzen
Die Umstellung Ihres Digitalen Zwillings von Plandaten auf reale Daten nach dem SOP ist ein entscheidender Schritt, um das volle Potenzial Ihrer Produktionsanlagen auszuschöpfen. Durch die frühzeitige Identifizierung von Optimierungspotenzialen können Sie nicht nur Ihre Effizienz steigern, sondern auch flexibel auf Veränderungen reagieren und Ihre Wettbewerbsfähigkeit langfristig sichern.
Nutzen Sie die Möglichkeiten des Digitalen Zwillings im Optimierungsbetrieb, um Ihre Fertigungsstrategien zu evaluieren, Leistungssteigerungen zu realisieren und sich erfolgreich in einem dynamischen Marktumfeld zu behaupten.
Von der Planung bis zur laufenden Produktion
Praxisbeispiel
Ausgangssituation
Auch kleine Verbesserungen bei der Ausbringungsmenge können über die Betriebszeit einer Fabrik zu erheblichen Mehreinnahmen führen. Jedoch ist das Testen von Optimierungsideen an der Echtanlage oft mit erheblichen Risiken und Kosten verbunden. Eventuell muss für die Umsetzung die Produktion stoppen und bereits funktionierende Prozesse müssen angepasst werden. Beeinflusst die geplante Verbesserung nicht das Bottleneck, hat die Optimierung keinen Einfluss auf die Ausbringungsmenge. Führt die geplante Optimierung in der Realität sogar zu einer Verschlechterung, muss neben den Kosten für die Umsetzung auch noch in den Rückbau investiert werden.
Einsatz
Hier liefert der Digitale Zwilling die optimale Lösung. Mit dem Digitalen Zwilling können Sie die Optimierungsansätze ohne Investitionskosten in Hardware und Produktionsstopps evaluieren. Anschließend werden nur die Investitionen getätigt, die im Hinblick auf die gesamte Produktion den gewünschten ROI bringen. Typische Fragestellungen, die mithilfe des Digitalen Zwillings beantwortet werden können, sind z. B.:
- Welche Produktmixe bringen die beste Performance auf der Anlage?
- Wie wirkt es sich auf die Gesamtanlagenleistung aus, wenn das Bottleneck 30 % schneller wird?
- Wo in der Anlage befindet sich nach dieser Leistungssteigerung das Bottleneck?
- Welche Anpassungen an den Steuerungsstrategien bringen einen erhöhten Durchsatz?
- Welche Performancesteigerung bringt eine neue Maschine an einer bestimmten Stelle in der Anlage?
- Reicht die Erweiterung, um eine weitere Produktionslinie aus, um die neuen Kunden beliefern zu können?
- Wie wirken sich aufwändige Bauteile auf die Gesamtperformance der Anlage aus?
Diese und viele weitere Fragen können mit Hilfe des Digitalen Zwillings beantwortet werden.
Vorteile
Damit ergeben sich für Sie folgende Vorteile:
- Die Produktion wird für Optimierungsexperimente nicht beeinflusst.
- Es fallen nur die Investitionskosten für die Hardware an, die auch benötigt wird.
- Es entsteht kein zusätzliches Risiko für Qualitätsverluste.
- Die Produktionsplanung kann auf die Performanceergebnisse zurückgreifen.
Weiteres Potenzial
Heutige Anlagen müssen immer wandlungsfähiger sein und sich an neue Kundenanforderungen und Produktentwicklungen anpassen. Unter “Anpassungen und Retrofits” zeigen wir Ihnen, wie Sie auch hier von einem Digitalen Zwilling profitieren können.