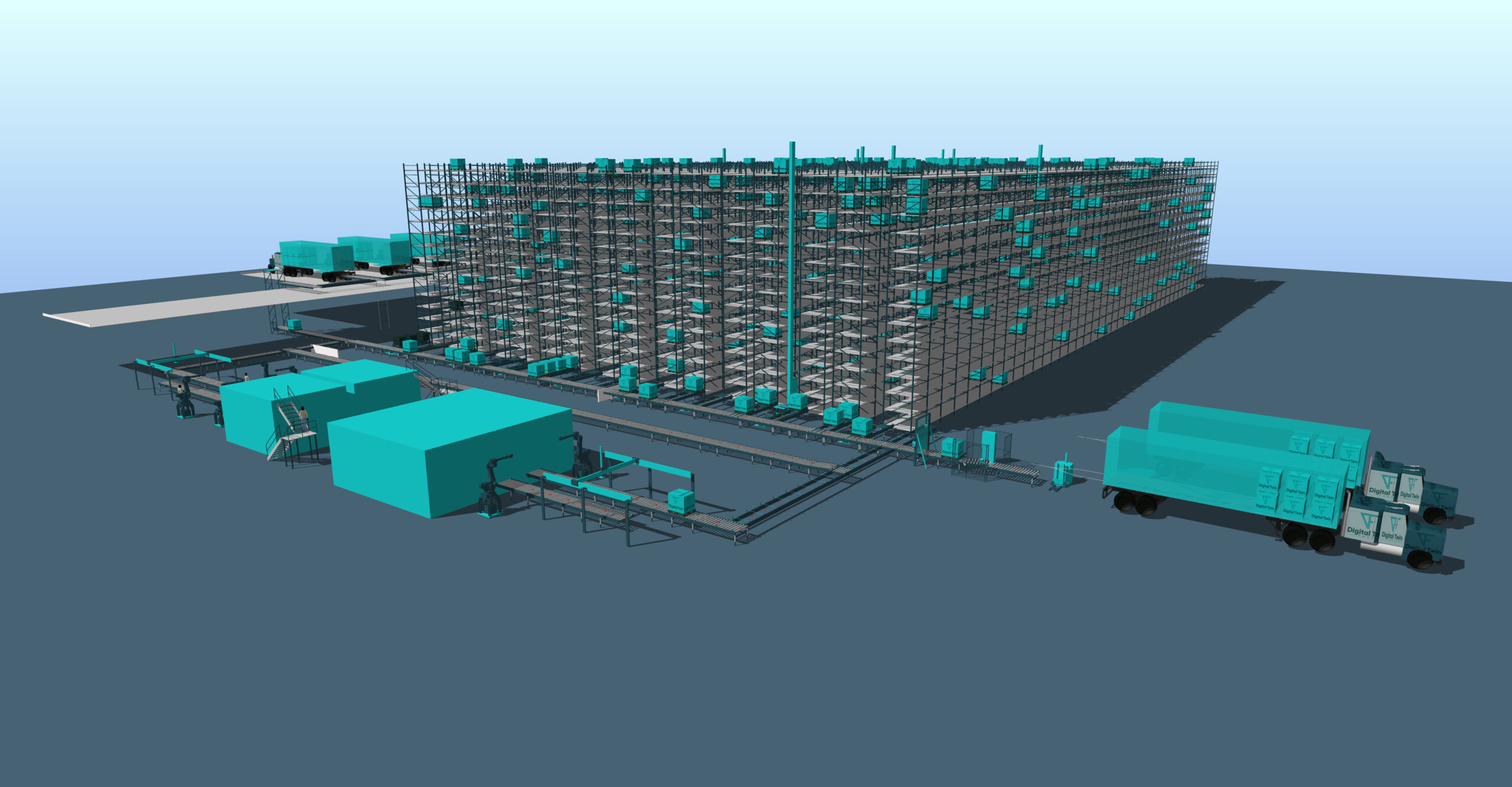
Digitaler Zwilling auf Fabrikebene
Grundlagen, Vorteile und praxisnahe Anwendungen des Digitalen Zwillings auf Fabrikebene.
Bei Fragen oder näherem Interesse buchen Sie gerne eine Demonstration.
Der Digitale Zwilling auf Fabrikebene hebt die industrielle Revolution auf ein neues Level. Er bildet nicht nur einzelne Maschinen, sondern komplette Produktionsstätten digital ab und ermöglicht so eine umfassende Analyse, Steuerung und Optimierung von Prozessen. Mit Echtzeitdaten und Simulationen lassen sich Abläufe verbessern, Ressourcen effizienter nutzen und Ausfallzeiten minimieren.
In diesem Artikel werfen wir einen Blick auf die Grundlagen, Vorteile und praxisnahe Anwendungen des Digitalen Zwillings auf Fabrikebene und zeigen, wie diese Technologie die Fabrik der Zukunft gestaltet.
Digitaler Zwilling auf Fabrikebene: Relevanz in der Fertigung
Der Digitale Zwilling gewinnt in der Fertigung zunehmend an Bedeutung, da er Unternehmen ermöglicht, physische Prozesse virtuell abzubilden, zu simulieren und zu optimieren. Durch die Integration von Echtzeitdaten aus der Produktion können Produktionsabläufe effizienter gestaltet, Stillstandszeiten minimiert und Ressourcen besser genutzt werden. Dies führt zu einer gesteigerten Produktivität, höherer Produktqualität und reduzierten Kosten – Faktoren, die in der modernen Industrie immer entscheidender werden, um wettbewerbsfähig zu bleiben. Die Möglichkeit, Szenarien vorab virtuell zu testen, fördert zudem Innovationen, da neue Ansätze risikoarm erprobt werden können.
Architektur eines Digitalen Zwillings auf Fabrikebene
Datenquellen und -integration
Digitale Zwillinge basieren auf einer Vielzahl von Datenquellen, die aus Sensoren, Maschinen und Fertigungsanlagen stammen. Sensoren erfassen kontinuierlich Echtzeitdaten, wie Temperatur, Druck oder Vibrationen, und liefern damit präzise Informationen über den aktuellen Zustand der physischen Anlage. Diese Daten werden dann mit Maschinensteuerungen und anderen Systemen der Fertigungsanlage integriert, um ein umfassendes Abbild des Produktionsprozesses zu erstellen. Die nahtlose Integration all dieser Datenquellen ermöglicht es, den Digitalen Zwilling immer aktuell zu halten und fundierte Entscheidungen zu treffen.
Datenmodellierung und -speicherung
Für die erfolgreiche Anwendung eines Digitalen Zwillings ist eine strukturierte Speicherung der Daten entscheidend. Hierbei werden die gesammelten Daten in Modellen organisiert, die die physischen Anlagen und Prozesse realitätsnah abbilden. Diese Modelle enthalten sowohl statische Daten, wie die Geometrie einer Maschine, als auch dynamische Daten, die sich mit der Zeit ändern, wie etwa der Zustand der Maschinenkomponenten. Wichtig ist es dabei, dass die Daten leicht zugänglich und konsistent sind, wodurch eine exakte Modellierung und Analyse der physischen Fertigung möglich wird.
Kommunikation und Netzwerke
Eine zuverlässige Kommunikation zwischen der realen Fabrik und ihrem Digitalen Zwilling ist unerlässlich, um eine präzise Synchronisation sicherzustellen. Diese Verbindung wird durch industrielle Netzwerke und Kommunikationsprotokolle ermöglicht, die dafür sorgen, dass die erfassten Echtzeitdaten direkt an das virtuelle Modell übertragen werden. Technologien wie OPC UA, MQTT oder 5G sorgen für eine sichere und schnelle Übertragung der Daten. Durch diese kontinuierliche Datenübertragung bleibt der Digitale Zwilling stets auf dem neuesten Stand, wodurch wiederum eine genaue Analyse und Steuerung der Fertigungsprozesse möglich wird.
Einsatzmöglichkeiten des Digitalen Zwillings
Optimierung der Produktion
Der Digitale Zwilling bietet erhebliche Vorteile bei der Optimierung der Produktion, indem er ermöglicht, potenzielle Engpässe frühzeitig zu erkennen und Maßnahmen zu ihrer Behebung zu ergreifen. Durch die Simulation von Produktionsszenarien können Effizienzsteigerungen identifiziert und umgesetzt werden, was zu einer besseren Ressourcennutzung und einer Reduzierung von Stillstandszeiten führt. Zudem können durch die Analyse von Echtzeitdaten Optimierungspotenziale schnell und gezielt aufgedeckt werden, wodurch Produktionsprozesse kontinuierlich verbessert werden.
Fehlererkennung und -prävention
Ein weiterer entscheidender Vorteil des Digitalen Zwillings liegt in der frühzeitigen Erkennung und Prävention von Fehlern. Durch die kontinuierliche Überwachung von Maschinendaten und die Simulation von Betriebszuständen können potenzielle Probleme frühzeitig erkannt und proaktive Wartungsmaßnahmen eingeleitet werden, bevor es zu teuren Ausfällen kommt. Die vorausschauende Diagnose und die Analyse von Verschleißmustern ermöglichen es, Maschinenprobleme zu antizipieren und gezielt einzugreifen, was die Zuverlässigkeit und Verfügbarkeit der Anlagen deutlich erhöht.
Produktionsplanung und -steuerung
Der Digitale Zwilling spielt auch eine zentrale Rolle in der Produktionsplanung und -steuerung. Durch die Möglichkeit, unterschiedliche Szenarien zu simulieren, können Entscheidungsträger fundierte Entscheidungen darüber treffen, wie Produktionsressourcen am besten eingesetzt werden sollten. Die Simulation von Produktionsabläufen ermöglicht es, Engpässe und potenzielle Probleme bereits im Planungsstadium zu identifizieren und alternative Lösungswege zu evaluieren. Dies führt zu einer höheren Flexibilität und einer verbesserten Anpassungsfähigkeit an veränderte Produktionsbedingungen oder Nachfrageschwankungen.
Schulungen und Mitarbeiterausbildung
Digitale Zwillinge bieten auch enorme Vorteile bei der Schulung und Ausbildung von Mitarbeitern. Durch die Simulation komplexer Abläufe und Maschinenprozesse können Mitarbeiter in einer sicheren, virtuellen Umgebung geschult werden, ohne dass das Risiko besteht, reale Anlagen zu beschädigen oder den Produktionsablauf zu stören. Dies ermöglicht eine praxisnahe Ausbildung und verbessert das Verständnis der Mitarbeiter für die Funktionsweise der Maschinen und Prozesse. Zudem können Trainingsszenarien gezielt auf individuelle Bedürfnisse angepasst werden, wodurch das Lernen effektiver gestaltet wird.
Vorteile des Digitalen Zwillings auf Fabrikebene
Transparenz und Echtzeitüberwachung
Der Digitale Zwilling verbessert die Transparenz von Fertigungsprozessen erheblich, indem er eine Analyse aller relevanten Produktionsparameter ermöglicht. Dadurch erhalten Entscheidungsträger und Produktionsleiter einen vollständigen Überblick über die Anlagen und Prozesse. Dies unterstützt dabei, potenzielle Probleme frühzeitig zu erkennen und zu beheben. Die erhöhte Transparenz trägt somit zu einer insgesamt effizienteren Steuerung der Produktion bei.
Kosteneffizienz
Der Einsatz eines Digitalen Zwillings trägt auch maßgeblich zur Kosteneffizienz in der Fertigung bei. Durch die frühzeitige Erkennung von Fehlern und die Optimierung der Inbetriebnahme können Ineffizienzen erheblich reduziert werden. Zudem wird durch die Minimierung von Ausfallzeiten bei Produktanpassungen und Retrofits die Produktivität erhöht, was wiederum zu einer Senkung der Gesamtbetriebskosten führt.
Flexibilität und Anpassungsfähigkeit
Der Digitale Zwilling ermöglicht es Unternehmen, flexibel und schnell auf Veränderungen am Markt zu reagieren. Echtzeitsimulationen helfen dabei, unterschiedliche Produktionsszenarien durchzuspielen und die beste Vorgehensweise zu identifizieren. Dadurch können Anpassungen an Produktionsprozesse rasch umgesetzt werden, was besonders in dynamischen Märkten mit schwankender Nachfrage von großem Vorteil ist. Diese Flexibilität trägt dazu bei, die Wettbewerbsfähigkeit zu erhalten und schnell auf Kundenbedürfnisse eingehen zu können.
Herausforderungen und Grenzen
Technologische Hürden
Trotz der zahlreichen Vorteile stehen Unternehmen bei der Implementierung von Digitalen Zwillingen vor einigen technologischen Hürden. Die Datensicherheit spielt eine entscheidende Rolle, da große Mengen an sensiblen Produktionsdaten erfasst und verarbeitet werden. Der Schutz dieser Daten vor unbefugtem Zugriff ist essenziell. Zudem ist die Interoperabilität zwischen verschiedenen Maschinen und Systemen eine Herausforderung, da oft unterschiedliche Hersteller und Protokolle beteiligt sind. Auch die technische Integration in bestehende IT- und OT-Systeme kann komplex sein und erfordert sorgfältige Planung und Umsetzung.
Kosten und Implementierung
Die Einführung eines Digitalen Zwillings erfordert eine beträchtliche Anfangsinvestition. Diese umfasst die Kosten für die erforderliche Hardware wie die notwendige IT-Infrastruktur sowie die Software zur Modellierung und Analyse. Zudem sind qualifizierte Fachkräfte erforderlich, um die Implementierung und den Betrieb zu gewährleisten. Die Höhe der Investitionskosten und der benötigten Ressourcen kann insbesondere für kleine und mittelständische Unternehmen eine Hürde darstellen. Dennoch bieten die Vorteile, wie erhöhte Effizienz und Kosteneinsparungen, eine gute Grundlage, damit sich die Investition schnell rentiert.
Datenmanagement
Der Digitale Zwilling basiert auf großen Mengen an Daten, die kontinuierlich erfasst, verarbeitet und gespeichert werden müssen. Das Management dieser Daten stellt eine Herausforderung dar, da nicht nur große Datenmengen gehandhabt werden müssen, sondern auch auf die Datenqualität geachtet werden muss. Eine hohe Datenqualität ist entscheidend, um zuverlässige Modelle und präzise Simulationen zu ermöglichen. Daher sind Systeme erforderlich, die eine zuverlässige Datenverarbeitung gewährleisten und gleichzeitig sicherstellen, dass die gesammelten Daten konsistent und aktuell sind.
Zukunftsaussichten und Trends
Künstliche Intelligenz und Machine Learning
Die Integration von Künstlicher Intelligenz (KI) und Machine Learning (ML) in den Digitalen Zwilling eröffnet neue Möglichkeiten zur intelligenten Steuerung und Optimierung von Fertigungsprozessen. KI-Algorithmen können Muster in den Produktionsdaten erkennen, Vorhersagen treffen und Optimierungsmaßnahmen vorschlagen. Dies ermöglicht es, den Digitalen Zwilling selbstlernend zu gestalten, sodass er im Laufe der Zeit immer präziser und effizienter wird. Durch die Nutzung von ML können Produktionsprozesse besser automatisiert und Entscheidungen datengetrieben getroffen werden.
Weiterentwicklung von IoT
Die Weiterentwicklung des Internets der Dinge (IoT) spielt eine zentrale Rolle für den Digitalen Zwilling. Immer mehr vernetzte Sensoren werden eingesetzt, um detaillierte Echtzeitdaten zu sammeln, die die Grundlage für noch genauere Digitale Abbilder bilden. Die kontinuierliche Erweiterung der IoT-Infrastruktur trägt dazu bei, die Genauigkeit und den Nutzen des Digitalen Zwillings zu steigern, indem eine größere Vielfalt an Produktionsparametern erfasst und analysiert werden kann.
Autonome Fabriken
Der Digitale Zwilling stellt eine Schlüsseltechnologie auf dem Weg zu vollständig autonomen Fabriken dar. Er ermöglicht die umfassende Überwachung, Steuerung und Optimierung von Produktionsprozessen, sodass Fabriken in Zukunft weitgehend selbstständig agieren können. Durch die Kombination von Echtzeitüberwachung, KI-gestützter Analyse und automatisierter Steuerung kann eine autonome Fabrik flexibel auf Veränderungen reagieren und nahezu ohne menschliches Eingreifen betrieben werden.